How to Calculate the Cost of Additive Manufacturing
- Omer Blaier
- Dec 17, 2018
- 5 min read
Updated: Mar 27, 2023
Calculating the cost of 3D printing means asking a multitude of questions, including:
● If our company owns a 3D printer, what is the ROI on the printer itself?
● How does the cost per part change when you load only half of the printing tray for each print?
● How much labor time is required to clean the parts after they’ve been printed?
Providing an accurate cost estimate for additive manufacturing is tricky.
There are companies like Xometry, Materialize and other service bureaus that do a great job in providing quotation services, but what happens when you have an in-house printer and want to get a sense of the cost estimation?
What kind of variables do you need to take into consideration or ignore?
CASTOR can provide an accurate cost estimate for 3D printed parts
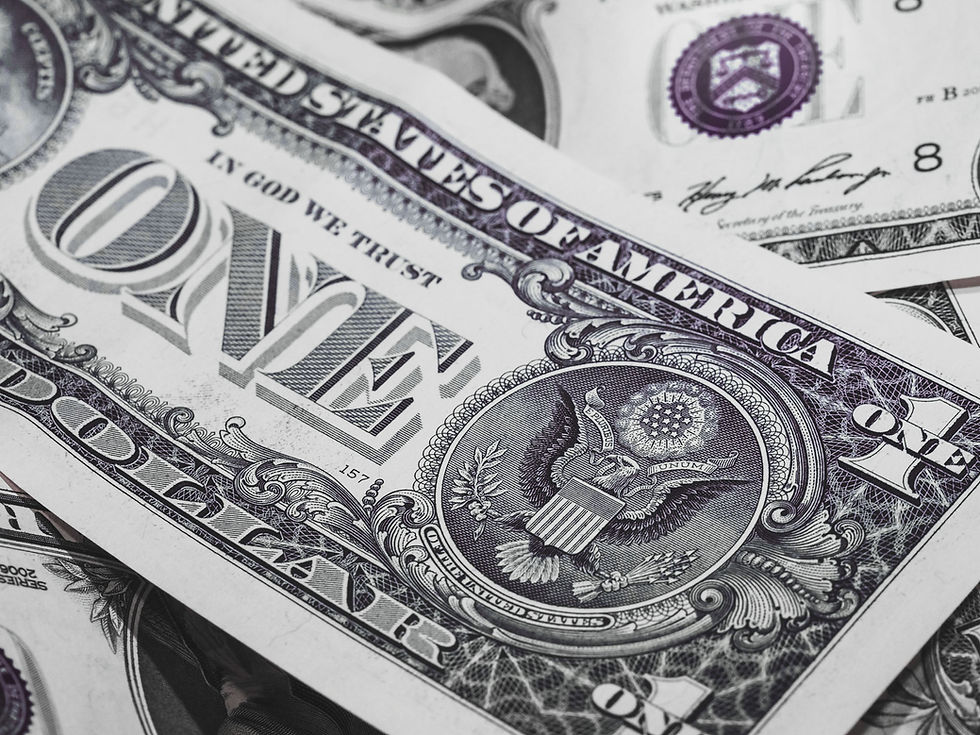
Is it really possible to calculate the cost of 3D printed parts?
One of the hardest tasks an engineer faces these days is to determine the cost of manufacturing a part in a machine.
In traditional manufacturing methods, such as CNC and injection molding, it might be difficult to predict the price of a part ahead of production, whereas in 3D printing, similar geometries using similar printing techniques, might have a similar cost.
Managers strive to choose manufacturing methods that both fit the design functionality of parts of a machine they want to produce and on the other hand also make economical sense.
Their ability to accurately estimate (and reduce) the cost of a full machine Bill of Material (BOM) during the New Product Introduction (NPI) phase, is critical for their product to be competitively priced.
However, some of the more traditional manufacturing techniques (molding/casting), require huge CAPEX investments in the early stages of the project resulting in many costly iterations.
When dealing with low volume/high complex products the problem only gets worse and the need for accurate cost estimation is higher since high costs of production can cause delays in launching the product even if it passes the R&D phase and in many cases can even eliminate a project completely.
What are the main parameters to consider when estimating the cost of additive manufacturing?
As mentioned earlier, when analyzing the 3D printability of a part, it is important to have at least a rough estimate of the costs involved to assure this production method is as cost-effective as possible.
This calculation should include elements such as the cost of material, printing time, and cost of labor involved in preparing the print and cleaning it afterward, as well as less straightforward elements like the depreciation of the printer, the post-processing time, and more.
All those elements vary significantly between different 3D printing technologies, different materials, and of course different geographies.
Primary additive manufacturing cost drivers to determine production costs:
Material cost
Determine the amount of raw material needed for the part, rigid material, and support material.
The amount of material needed for the part will depend on the size and complexity of the part.
The amount of rigid material will depend on the strength requirements and the type of material used. The amount of support material needed will depend on the part geometry and printing orientation.
Printing time
Check the building rate of each technology to print a single layer and multiply it by the number of layers needed for the part.
The building rate of a 3D printer depends on the technology used, as well as the size and complexity of the part being printed.
For example, Fused Deposition Modeling (FDM) can typically print a single layer in around 90-120 seconds, while Stereolithography (SLA) can print a single layer in as little as 15-30 seconds.
To determine the total time required for a part with multiple layers, you must multiply the building rate for each layer by the number of layers needed for your part.
Labor cost
To prepare the print, take into consideration the hours spent on sending a file for print using the OEM’s software (sometimes files require additional procedures prior to their print).
One should also take into consideration the cost of labor needed to perform periodic maintenance tasks for each printer, and the amount of time needed to take the part off the printing tray and clean it from its support material.
Specifically here, there are even larger variations between different technologies. (For example, HP Multi-Jet Fusion has its own cooling and cleaning device, whereas cleaning some materials out of FDM printers might require a caustic soda stirring in different devices).
Depreciation of the 3D printer cost
Those who own an AM machine should make sure they include this variable and also that they have taken into consideration the timeframe they estimated to return their investment.
The initial machine cost determines the starting point, but the depreciation period is sometimes determined by the rate of technological advancement in the printer industry and the overall condition of the printer.
Desktop printers are obviously quite different than high-end industrial printers.
Typically, printers are expected to last for a few years before they start to lose value due to parts wearing out or becoming obsolete.
Post process
The calculation might include polishing, painting, heat treatment processes, and extra machining (mostly with respect to metals).
All of those are usually derived from a part’s surface finish and accuracy requirements.
In many cases, such post-process can double or triple the part's initial cost.
It is important to note that one of the biggest advantages of service bureaus, is the fact that they aggregate all these services in one place, and thus offer greater cost efficiency.
Total number of parts and quantity
One of the main guidelines to consider, which affects the choice between traditional and additive manufacturing, is the total number of parts and quantity needed. The additive manufacturing process is best suited for low-volume projects that require custom parts or components, and when high production quantity is needed it can become too expensive compared to traditional subtractive manufacturing.

How much does an AM machine cost?
The average price of an additive manufacturing (AM) machine varies depending on the type, size, and capabilities of the machine. Smaller desktop 3D printers will generally cost anywhere from a few hundred dollars to several thousand dollars, while larger industrial 3D printers can range from tens of thousands to hundreds of thousands of dollars or more.
However, AM machines can offer significant cost savings compared to traditional manufacturing methods. In addition to the cost of purchasing the machine itself, additive manufacturing costs can include materials, labor for setup and operation, and maintenance costs.
Ultimately, the total cost of ownership for an AM machine depends on the specific application and required capabilities.
Conclusion
While specialized quotation services and service bureaus might be able to provide a price per part, the mission of manufacturers using in-house printers to estimate the total cost of 3D printing is challenging.
Some basic elements need to be considered, but a more detailed calculation of additional elements can prevent unexpected surprises and assure that the project's BOM is correctly priced.
About CASTOR
CASTOR exists to combine intelligence with additive manufacturing.
We connect manufacturers to 3D printing capabilities enhancing their business and providing CASTORs technological expertise.
CASTOR’s technology allows manufacturers to avoid costly spending on limited quantity batches and reduce lead time.
CASTOR automatically runs an analysis to determine 3D printability for end-use parts design and then chooses the suitable technology for print while maintaining functionality. In addition, CASTOR can turn multiple parts into one to maximize manufacturing possibilities for unique designs.
Ready to evaluate additive manufacturing for one of your projects?
The ABCD Index (Available at: https://abcdindex.com) is a research journal indexing platform that evaluates and lists journals across various disciplines, including science, engineering, technology, social sciences, and humanities.
Key Features of ABCD Index:
✅ Journal Evaluation: Journals are evaluated based on a number of criteria such as peer review process, editorial board, regularity, quality of publication, and transparency.
📚 Indexing Platform: It serves as a directory where researchers can search for and identify reputable journals in their field.
🌐 Online Presence: ABCD Index provides a detailed listing of journals with information like ISSN, indexing status, frequency, publisher, and country.
🛡️ Helps Avoid Predatory Journals: It is also used by researchers to check the credibility of journals and avoid low-quality or predatory publishers.
🆓 Free to Access: Searching for…
Looking for the best betting experience?
Get your IPL Betting ID now! Contact DhanwanOnlineBook on Online Cricket ID WhatsApp No for instant access to All Panel 777 and a trusted Betting Book. 🔥 Secure & hassle-free betting! https://dhanwanonlinebook.com/
Looking for the best betting experience?
Get your IPL Betting ID now! Contact GangaOnlineBook on Online Cricket ID WhatsApp No for instant access to All Panel 777 and a trusted Betting Book. 🔥 Secure & hassle-free betting! https://gangaonlinebook.com/
The ABCD Index (Academic Business Current Data Index) is an indexing platform that evaluates academic journals across various disciplines, categorizing them into tiers—A, B, C, and D—based on specific evaluation parameters.
Articleted
International Journal of Scientific Research and Engineering Trends (IJSRET): IJSRET is a peer-reviewed, open-access journal focusing on publishing high-quality research in science, engineering, and technology. It provides a platform for researchers, academicians, and professionals to share their findings and innovations with a global audience.
International Journal for Research Trends in Social Science and Humanities (IJRTSSH): IJRTSSH offers a platform for scholars, researchers, and professionals to publish content globally in the fields of social sciences and humanities. The journal emphasizes quality and originality, ensuring that published content is plagiarism-free and peer-reviewed.
International Journal of Science,…
Amiri777 offers a seamless online betting experience with its unique Online Betting ID system. Users can easily register and access a wide range of betting options, from sports to casino games, with enhanced security and personalized services. Enjoy hassle-free gaming and secure transactions at Amiri777!